Can I Make Titanium Damascus? Part 3
Entertainment
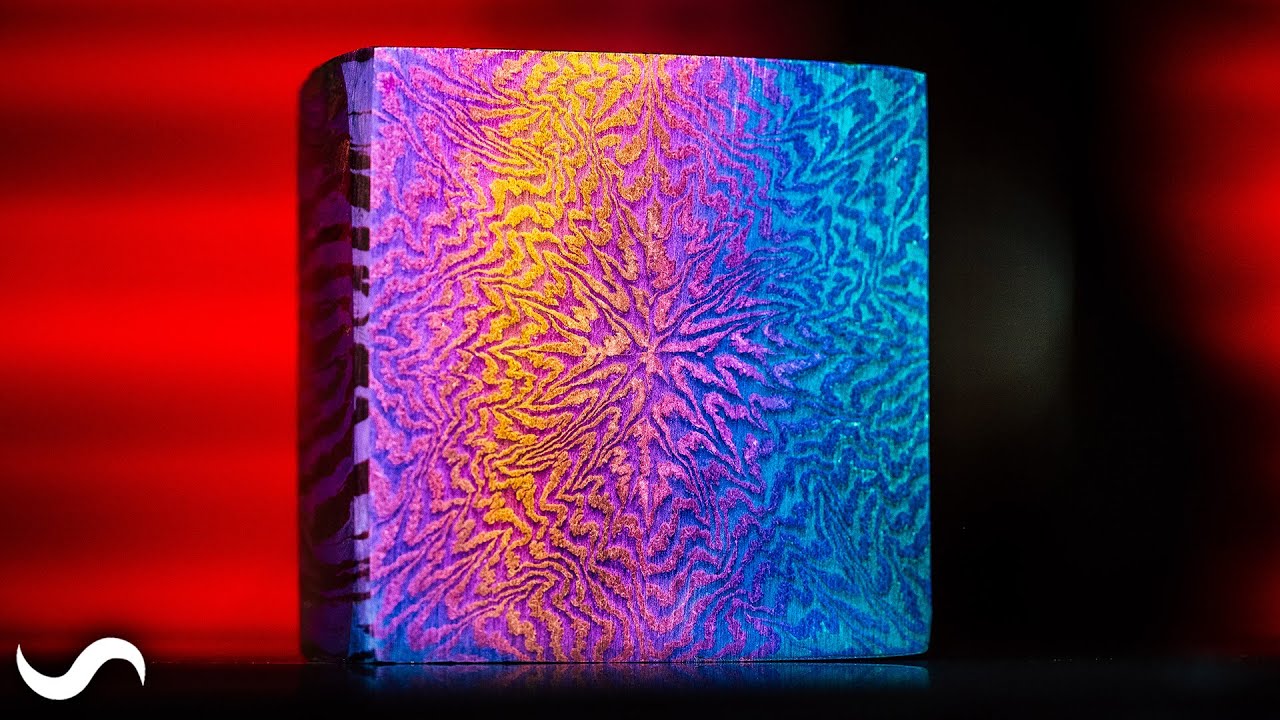
Introduction
Welcome back to our journey of creating awesome titanium Damascus! In the previous episode, we discovered that twisting titanium doesn't result in disaster, and we successfully made two rings. In this episode, we will explore whether we can forge patent-welded titanium into mosaic patterns. While the last episode focused on the exterior design, mosaics are about the end grain patterns that we can create.
Experimenting with Billet B
You may recall that I welded up a second billet at the start of the last episode. Billet B is the subject of our experiments today. After cutting off the mild steel jacket, it's time to forge it into a round bar and position the layers on end. We’ll then smush them together to see how the titanium copes with this mosaic pattern development.
[Applause]
[Music]
After smushing the layers, I was surprised by the results. The sides of the pattern were flatter than expected; usually, they feature more aggressive curves. However, I’m pleased to report that we are within 0.4 mm of the intended width and thickness! Forging freehand with my hammer has yielded impressive technical results despite the challenges of machining this difficult material.
Annealing Titanium
Next, I wanted to ensure I had the best information regarding annealing titanium. Annealing softens metals, making them easier to machine. However, different grades of titanium, specifically commercially pure grade 2 and 6-4V (grade 5), anneal at slightly different temperatures. The appropriate temperatures for aging these materials are as follows:
- Grade 5: 690 to 760 °C for half an hour to 2 hours
- Grade 2: 538 to 704 °C for half an hour to 2 hours
We settled on 710 °C for our annealing process, a temperature that all grades can accommodate.
Milling Titanium Damascus
After annealing, it was time to clean up the titanium. Our first attempt at milling wasn't spectacular, but I received valuable advice from a machine tooling supplier. They recommended specific inserts designed for cutting titanium rather than generic ones. This improvement fueled my hope for a better milling experience.
It also became evident that to enhance cut performance, we needed to use coolant effectively. I found the coolant pump in my workshop, and although it was filled with sludge, I managed to clean it out and prepare it for use.
[Music]
When I switched to the newly recommended face milling inserts, the difference was remarkable. The surface finish was incredible, and we achieved excellent results with reduced costs on inserts.
It’s always exciting to receive fresh supplies, and this time, I had two sheets of 2 mm titanium delivered to the workshop, costing approximately £2,500! My plans for this titanium Damascus are ambitious, and I’m excited to embark on the next steps.
Workholding Solutions
As part of our experiments, I designed a custom fixture that would allow me to hold pieces of titanium that had limited material for clamping. This solution proved effective and allowed for precise cuts with our band saw, achieving a variation of up to 0.4 mm.
After successfully creating a cutting fixture, I looked at the patterns that emerged after forging and was happy to see some beautiful zigzagging designs.
Anodizing and Finalizing the Pattern
Next, I aimed to anodize the titanium to produce colorful results. This process involves a three-step approach: cleaning the titanium, etching, and anodizing using a DC power supply. While attempting to anodize, we initially faced issues with the titanium oxide layer preventing effective bonding. After grinding off the layers and cleaning up the surfaces, we achieved stunning results with vibrant colors.
[Music]
In conclusion, the journey of exploring titanium Damascus continues to unravel new possibilities. This process has opened doors to exciting future projects, and I can't wait to share what’s next.
Be sure to check out today's sponsor, and I’ll see you in the next episode!
Keyword
titanium, Damascus, billet, forging, mosaic patterns, annealing, milling, coolant, anodizing, surface finish
FAQ
Q1: What is titanium Damascus?
A1: Titanium Damascus is a layered material made from different grades of titanium, forged together to create unique patterns, similar to traditional steel Damascus.
Q2: What temperatures are required for annealing titanium grades?
A2: Grade 5 titanium anneals at 690 to 760 °C, while Grade 2 titanium requires 538 to 704 °C, both for half an hour to 2 hours.
Q3: Why is coolant important when machining titanium?
A3: Coolant is essential because titanium does not conduct heat well. Using coolant helps prevent overheating of the workpiece during machining.
Q4: How can you anodize titanium?
A4: Anodizing titanium involves cleaning the surface, etching it to remove oxides, and applying an electrical current in an electrolyte solution to achieve vibrant colors.
Q5: What were the challenges faced while milling titanium Damascus?
A5: Initial milling attempts resulted in a poor surface finish and damage to inserts, leading to the search for specialized tooling recommendations that ultimately improved the results.